Four Key Tips to Avoid Overspending Your Budget for STOs
STOs, or shutdowns, turnarounds, and outages, are a critical part of maintenance strategies for most manufacturing and production facilities. These activities help to ensure the continuous and reliable operation of assets so that there are no unplanned stoppages in production. However, STOs also come with a major undertaking and expenditure. They can command significant capital and operating budgets, attract the attention of shareholders and board of directors, and impact inventory supply chains and customer relationships. Therefore, it is essential to optimize STOs and avoid overspending your budget.
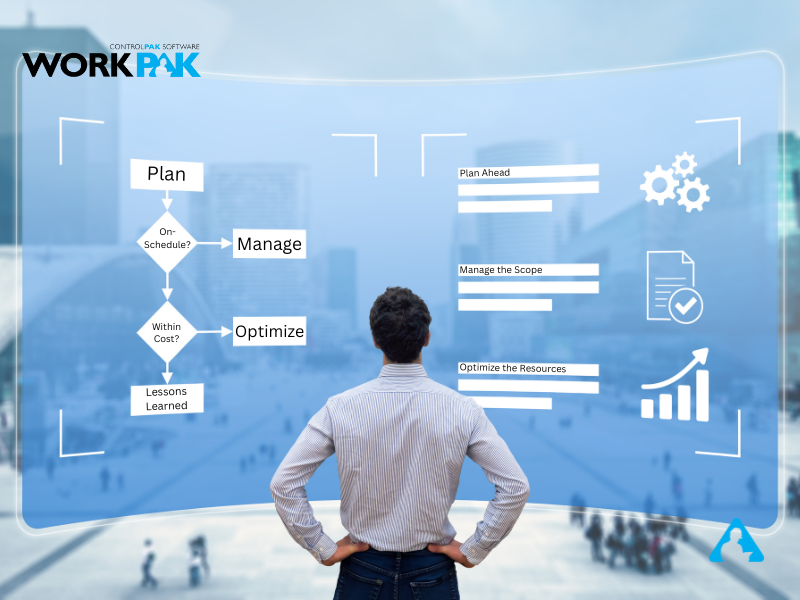
Here are four key tips on how to do that:
Plan ahead. Plan STOs about 18-24 months in advance and involve all the relevant stakeholders, such as maintenance, engineering, operations, procurement, safety, quality, and contractors. The more time the team plans the STO will lead to a better and more predictable execution plan. Define a detailed scope of work, schedule, and budget and agree upon these areas by all parties. In WorkPAK, build your scope of work, durations for the schedule, and budget estimates right within the program. Plan your work and review potential risks, contingencies, and opportunities for improvement collaboratively with your stakeholders and STO teams.
Manage the scope. One of the main reasons for STO budget overruns is scope creep, or the addition of unplanned or unnecessary work during the execution phase. To avoid this, clearly communicate and approve the scope of work and any changes by a designated authority to all involved. Prioritize the scope based on the criticality, urgency, and feasibility of the tasks. Evaluate any emergent work discovered during inspection and justify it before adding to the scope. Our Change Management feature in WorkPAK helps you organize and make decisions on scope changes and urgency, ensuring all parties agree to pursue the required changes during the execution phase.
Optimize the resources. Another major factor that affects the STO budget is the availability and utilization of resources, such as labor, materials, tools, and equipment. WorkPAK provides a summary of the resources required for your STO with an outlook and estimate of timelines, quantities, and number of personnel will be on-hand to execute the scope of work. To optimize the resources and using our WorkPAK resource reports and dashboards, take the following steps to support your STO timeline:
- Secure the required resources in advance and ensure delivery of procurement items on time.
- Use vendor standardization and inventory management to reduce the costs and complexity of procurement.
- Leverage innovative technologies with the help of WorkPAK, such as advanced analytics, digital plan tools in WorkPAK, and connect links and videos from drones, to enhance the efficiency and quality of work.
- Train and supervise the workforce, especially the contractors, to ensure that they follow the best practices and safety standards. Add safety requirements and blinding details to WorkPAK’s work packages to review with the workforce.
- Monitor and control the resource consumption and performance during the STO and adjust accordingly. Use WorkPAK’s timesheets, material, rentals, and tool management features to track materials and resources on-hand and ensure their productivity against your baseline manhours and durations meet your expectations.
Learn from the experience. After completing the STO, conduct a thorough review and analysis to evaluate the results and identify the lessons learned. Measure key performance indicators, such as safety, quality, schedule, and cost, and compare with the planned targets. Identify the root causes of any deviations, issues, or failures should be determined and implement corrective actions. Document the best practices, success stories, and feedback and share for future reference and improvement. Track your lessons learned of specific job scopes in WorkPAK and utilize your previous STO scope of work and activity templates to save you time and effort planning your next STO.
By following these tips and leveraging our WorkPAK software, you can avoid overspending your budget for STOs and make the most of the rare opportunities that scheduled downtime provides. STOs can be a source of competitive advantage for your organization when managed effectively and efficiently. Remember, STOs are not just maintenance and engineering events, they are whole business events that require strategic thinking and collaboration. WorkPAK makes it easier for you to collaborate and apply your strategies to achieve successful STOs. Find out more about WorkPAK. Request a software demo.